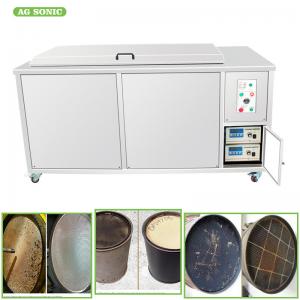
Add to Cart
Dpf Industrial Ultrasonic Cleaner For Radiator Truck Dpf Filters Clean
How to Clean Filters with Ultrasonic Energy
Operating an Ultrasonic Filter Cleaner System
Ultrasonic cleaners are available in numerous sizes based on the capacity of the cleaning solution tank, and can range from tabletop models to industrial-sized floor models. Regardless of size they are equipped with ultrasonic generators that excite tank-mounted transducers that create millions of microscopic bubbles in the cleaning solution. These implode on contact with the filters being cleaned to blast away contaminants from any surface wetted by the ultrasonic cleaning solution. Depending on models, ultrasonic filter cleaning equipment such as available have timers, temperature controllers, sweep and degas options. Rinse stations and drying stations are also available for assembly line filter cleaning.
Here’s a simplified series of operation steps for ultrasonic filter cleaning equipment. Modifications can be made based on specific filter cleaning requirements.
1. Add water to the fill line of the ultrasonic cleaning tank and prepare the ultrasonic cleaning solution clean A4 diluted to 2-5% with water. This is formulated for cleaning stainless and carbon steel, copper, brass and plastic.
2. Turn on the ultrasonic cleaner and degas function to both mix and degas the solution. Degassing removes air trapped in the water, which inhibits the cleaning operation. If the cleaner does not have a degas function allow it to run until bubbles stop coming to the surface.
3. Once degassing is complete you’re ready to clean the filters. Set the temperature to about 70°C for metal filters or about 50°C for plastics and the timer to 10 minutes. Experience will tell you the optimum temperature and how much time is required for your particular filter cleaning operations.
4. Place the filters in the cleaning basket so they do not contact each other, lower them into the ultrasonic cleaning solution, turn the unit on and activate the sweep function if so equipped. This evenly distributes the cavitation action throughout the solution for more uniform cleaning.
5. At the end of the cleaning cycle remove and inspect the filters. If they appear clean, rinse and dry. Depending on filter design you can either air blow dry or place them into a drying oven.
6. Apply a filter coating if required. The filters are now ready for reuse.
Ultrasonics efficiently removes:
Ultrasonics can clean a wide range of filters including:
Benefits of ultrasonics for filters:
Fllter Ultrasonic Cleaner Specifications:Ultrasonic Cleaning and Drying
Features:
Specifications for ultrasonic cleaner T-90S | |
Model | T-90S |
Tank capacity | 540L |
Tank size | 1000x800x700mm |
Unit size | 1140x940x920mm |
Tank material | 2mm SUS304 |
Ultrasonic power | 4500W |
Heating power | 12KW |
Timer | 1-99min adjustable |
Heater | 0-80c adjustable |
Frequency | 28/40khz |
Control | External generator, more stable |
Optional | Oil filter system, pneumatic lift, rinsing tank, etc. |
Voltage | 110V, 1phase; 220V, 3phases/220V, 1phase; 380V, 3phases |
Warranty | 1 year |
Packing | 1unit/wooden case |
Diesel Particulate Filter Ultrasonic Cleaning Effect
Features of the machine:
• Low maintainence machine
• Heavy duty cleaning systems
• Chemical friendly- SS Rust proof body
• Industrial guage farication, build to last
• One year warrenty on any manufacturing defect
• Completely customized to suit the cleaning requirement
• Less human interfearance and less scope of error
• Accurate and uniform cleaning everytime
How the System Operates:
The system operates in the following manner:
In a process termed "cavitation", micron-size bubbles form and grow due to alternating positive and negative pressure waves in a solution. The bubbles subjected to these alternating pressure waves continue to grow until they reach resonant size. Just prior to the bubble implosion, there is a tremendous amount of energy stored inside the bubble itself. Temperature inside a cavitating bubble can be extremely high, with pressures up to 500 atm. The implosion event, when it occurs near a hard surface, changes the bubble into a suction jet about one-tenth the bubble size, which travels at speeds up to 400 km/hr away from the hard surface. With the combination of pressure, temperature, and velocity, the jet frees contaminants from their bonds with the substrate. Because of the inherently small size of the jet and the relatively large energy, ultrasonic cleaning has the ability to reach into small crevices and remove entrapped soils very effectively.